液体火箭发动机的四种主要循环方式
来源:百度文库 编辑:超级军网 时间:2024/04/29 17:41:16
燃气发生器循环
Gas-generator cycle: The gas-generator cycle, also called open cycle, taps off a small amount of fuel and oxidizer from the main flow (typically 3 to 7 percent) to feed a burner called a gas generator. The hot gas from this generator passes through a turbine to generate power for the pumps that send propellants to the combustion chamber. The hot gas is then either dumped overboard or sent into the main nozzle downstream. Increasing the flow of propellants into the gas generator increases the speed of the turbine, which increases the flow of propellants into the main combustion chamber, and hence, the amount of thrust produced. The gas generator must burn propellants at a less-than-optimal mixture ratio to keep the temperature low for the turbine blades. Thus, the cycle is appropriate for moderate power requirements but not high-power systems, which would have to divert a large portion of the main flow to the less efficient gas-generator flow.
As in most rocket engines, some of the propellant in a gas generator cycle is used to cool the nozzle and combustion chamber, increasing efficiency and allowing higher engine temperature.
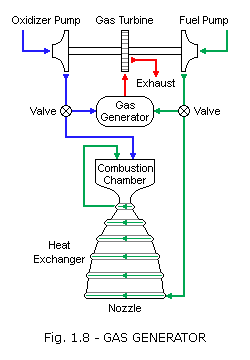
燃气发生器循环
Gas-generator cycle: The gas-generator cycle, also called open cycle, taps off a small amount of fuel and oxidizer from the main flow (typically 3 to 7 percent) to feed a burner called a gas generator. The hot gas from this generator passes through a turbine to generate power for the pumps that send propellants to the combustion chamber. The hot gas is then either dumped overboard or sent into the main nozzle downstream. Increasing the flow of propellants into the gas generator increases the speed of the turbine, which increases the flow of propellants into the main combustion chamber, and hence, the amount of thrust produced. The gas generator must burn propellants at a less-than-optimal mixture ratio to keep the temperature low for the turbine blades. Thus, the cycle is appropriate for moderate power requirements but not high-power systems, which would have to divert a large portion of the main flow to the less efficient gas-generator flow.
As in most rocket engines, some of the propellant in a gas generator cycle is used to cool the nozzle and combustion chamber, increasing efficiency and allowing higher engine temperature.
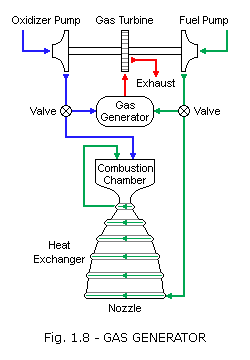
分级燃烧循环
Staged combustion cycle: In a staged combustion cycle, also called closed cycle, the propellants are burned in stages. Like the gas-generator cycle, this cycle also has a burner, called a preburner, to generate gas for a turbine. The preburner taps off and burns a small amount of one propellant and a large amount of the other, producing an oxidizer-rich or fuel-rich hot gas mixture that is mostly unburned vaporized propellant. This hot gas is then passed through the turbine, injected into the main chamber, and burned again with the remaining propellants. The advantage over the gas-generator cycle is that all of the propellants are burned at the optimal mixture ratio in the main chamber and no flow is dumped overboard. The staged combustion cycle is often used for high-power applications. The higher the chamber pressure, the smaller and lighter the engine can be to produce the same thrust. Development cost for this cycle is higher because the high pressures complicate the development process. Further disadvantages are harsh turbine conditions, high temperature piping required to carry hot gases, and a very complicated feedback and control design.
Staged combustion was invented by Soviet engineers and first appeared in 1960. In the West, the first laboratory staged combustion test engine was built in Germany in 1963.
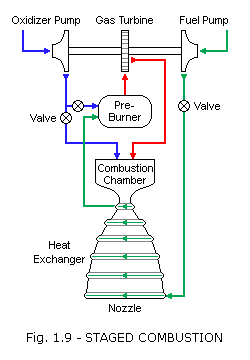
分级燃烧循环
Staged combustion cycle: In a staged combustion cycle, also called closed cycle, the propellants are burned in stages. Like the gas-generator cycle, this cycle also has a burner, called a preburner, to generate gas for a turbine. The preburner taps off and burns a small amount of one propellant and a large amount of the other, producing an oxidizer-rich or fuel-rich hot gas mixture that is mostly unburned vaporized propellant. This hot gas is then passed through the turbine, injected into the main chamber, and burned again with the remaining propellants. The advantage over the gas-generator cycle is that all of the propellants are burned at the optimal mixture ratio in the main chamber and no flow is dumped overboard. The staged combustion cycle is often used for high-power applications. The higher the chamber pressure, the smaller and lighter the engine can be to produce the same thrust. Development cost for this cycle is higher because the high pressures complicate the development process. Further disadvantages are harsh turbine conditions, high temperature piping required to carry hot gases, and a very complicated feedback and control design.
Staged combustion was invented by Soviet engineers and first appeared in 1960. In the West, the first laboratory staged combustion test engine was built in Germany in 1963.
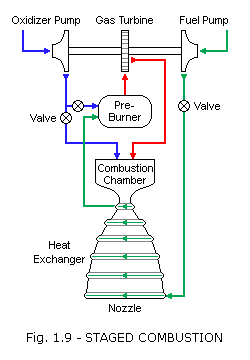
膨胀循环
Expander cycle: The expander cycle is similar to the staged combustion cycle but has no preburner. Heat in the cooling jacket of the main combustion chamber serves to vaporize the fuel. The fuel vapor is then passed through the turbine and injected into the main chamber to burn with the oxidizer. This cycle works with fuels such as hydrogen or methane, which have a low boiling point and can be vaporized easily. As with the staged combustion cycle, all of the propellants are burned at the optimal mixture ratio in the main chamber, and typically no flow is dumped overboard; however, the heat transfer to the fuel limits the power available to the turbine, making this cycle appropriate for small to midsize engines. A variation of the system is the open, or bleed, expander cycle, which uses only a portion of the fuel to drive the turbine. In this variation, the turbine exhaust is dumped overboard to ambient pressure to increase the turbine pressure ratio and power output. This can achieve higher chamber pressures than the closed expander cycle although at lower efficiency because of the overboard flow.
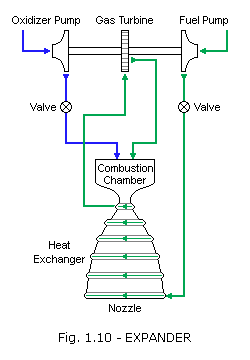
膨胀循环
Expander cycle: The expander cycle is similar to the staged combustion cycle but has no preburner. Heat in the cooling jacket of the main combustion chamber serves to vaporize the fuel. The fuel vapor is then passed through the turbine and injected into the main chamber to burn with the oxidizer. This cycle works with fuels such as hydrogen or methane, which have a low boiling point and can be vaporized easily. As with the staged combustion cycle, all of the propellants are burned at the optimal mixture ratio in the main chamber, and typically no flow is dumped overboard; however, the heat transfer to the fuel limits the power available to the turbine, making this cycle appropriate for small to midsize engines. A variation of the system is the open, or bleed, expander cycle, which uses only a portion of the fuel to drive the turbine. In this variation, the turbine exhaust is dumped overboard to ambient pressure to increase the turbine pressure ratio and power output. This can achieve higher chamber pressures than the closed expander cycle although at lower efficiency because of the overboard flow.
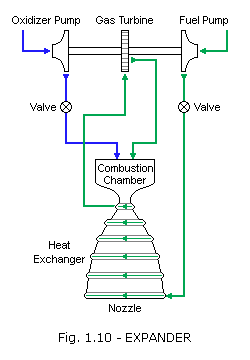
挤压循环
Pressure-fed cycle: The simplest system, the pressure-fed cycle, does not have pumps or turbines but instead relies on tank pressure to feed the propellants into the main chamber. In practice, the cycle is limited to relatively low chamber pressures because higher pressures make the vehicle tanks too heavy. The cycle can be reliable, given its reduced part count and complexity compared with other systems.
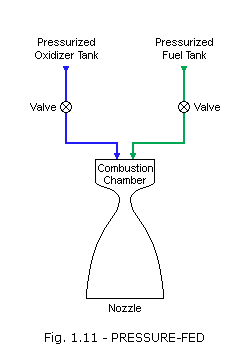
挤压循环
Pressure-fed cycle: The simplest system, the pressure-fed cycle, does not have pumps or turbines but instead relies on tank pressure to feed the propellants into the main chamber. In practice, the cycle is limited to relatively low chamber pressures because higher pressures make the vehicle tanks too heavy. The cycle can be reliable, given its reduced part count and complexity compared with other systems.
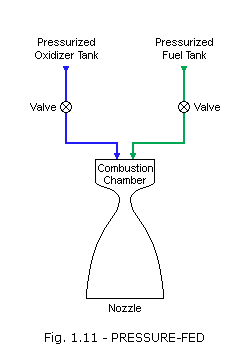
求翻译;funk
原帖由 zhyzq 于 2008-2-11 16:12 发表
求翻译;funk
这么简单浅显的英文都看不懂?
原帖由 dark_knight 于 2008-2-11 22:40 发表
这么简单浅显的英文都看不懂?
:lol 也不是,应该是比较多人包括我平时没有看大量英文资料的习惯,不能很通畅的读下来,:D 收藏下来花半个小时慢慢看一下
原帖由 dark_knight 于 2008-2-11 22:40 发表
这么简单浅显的英文都看不懂?
你懂不代表别人懂啊?你水平高,别人看起来费力,所以为了普及大众,外语材料最好翻译一下,哪怕是粗略的翻译也可以.
土鳖貌似都素最后一个:D
前三种有蜗轮泵,最后一种没有:D
原帖由 bigblu 于 2008-2-12 13:03 发表
前三种有蜗轮泵,最后一种没有:D
你要这么说也没错,在Sutton和Biblarz的Rocket Propulsion Elements第七版中,就把液体火箭发动机分为两大类,一类是涡轮泵增压的,另一类是吹气增压的
液体火箭发动机的涡轮泵设计本身就是一个专项,也分为好多种形式。涡轮有在氧化泵和燃料泵一侧的,也有在氧化泵和燃料泵之间的,还有涡轮通过减速齿轮组分别驱动氧化泵和燃料泵的,或者氧化泵和燃料泵由两个独立的涡轮各自驱动,再有就是高低压涡轮分别驱动高低压泵。
:handshake哪 一类最有发展前途???哪一类最先进???
]]
这还用翻译,一看图就明白,第一个是燃器涡轮泵输送能力最强,第2个和第3个利用燃料热膨胀驱动,输液差点,最后那是靠燃料和氧化跻罐内压力输送的.
挤压循环貌似也有用压缩氮气提供压力的吧?:o
原帖由 bigblu 于 2008-2-12 13:00 发表
土鳖貌似都素最后一个:D
这是打哪儿说起?
图配错了。
膨胀循环配成了燃气发生器循环的系统图
挤压循环配上了分级燃烧循环的图
膨胀循环配成了燃气发生器循环的系统图
挤压循环配上了分级燃烧循环的图
好文!但是看不懂![:a6:]
LZ图配的顺序不对啊,3楼配的图是燃气发生器循环,4楼是分级燃烧循环。另外求此完整资料
回复 9# bigblu
报告老大,TG的除了在研的某几种外,现役的主要是第二种
报告老大,TG的除了在研的某几种外,现役的主要是第二种
海之魂 发表于 2010-5-23 23:46 
当时用的是链接盗图,现在人家的网页调整了,都乱了

当时用的是链接盗图,现在人家的网页调整了,都乱了
这个帖子已经很老了,下次再详细展开
直接链摆渡百科里面的图吧,那个的标注好歹是汉字的。
现在的图是对的啊